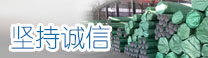
行業(yè)動態(tài)
聯(lián)系方式
聯(lián)系人: 劉經(jīng)理
手 機 :136 7673 1206
電 話 : 0577-28909778
E-mail : myzhide@126.com
大口徑不銹鋼管
您的位置:網(wǎng)站首頁 > 新聞動態(tài) > 大口徑不銹鋼管 > 正文多位一體不銹鋼冶煉在太鋼的生產(chǎn)與實踐
通過分析太鋼不銹鋼原料鉻鎳生鐵、高碳鉻鐵、鐵水等的特性以及研究了原料中Si、C元素優(yōu)化使用,采用中頻爐、電弧爐、轉(zhuǎn)爐、AOD等工序進行多種組合,開發(fā)了300系400系鋼種多條不同組合的不銹鋼工藝路線,形成了多位一體不銹鋼生產(chǎn)工藝。生產(chǎn)實踐表明,400系不銹鋼采用180t轉(zhuǎn)爐脫磷鐵水+50t中頻爐熔化高碳鉻鐵預熔液兌入AOD冶煉的工藝,鉻收得率提高2.47%,硅鐵消耗降低5.5kg/t,石灰消耗降低10kg/t,300系不銹鋼采用160t電弧爐+2×50t中頻爐熔化預熔液兌入AOD冶煉工藝,鉻收得率提高2.2%,電極消耗降低1.8kg/t,大幅降低了冶煉成本。
不銹鋼指在大氣和酸、堿、鹽等腐蝕性介質(zhì)中呈現(xiàn)鈍態(tài)、耐蝕而不生銹的含鉻合金鋼,其中Cr含量10.5%~30%。因其優(yōu)異的耐腐蝕性和優(yōu)良的綜合性能,廣泛應用于各工業(yè)和民用領域。2018年全球不銹鋼粗鋼產(chǎn)量5070萬t,中國不銹鋼產(chǎn)量達2670萬t,占全球產(chǎn)量的52.3%,中國不銹鋼表觀消費量為2210萬t。
隨著低品位紅土鎳礦生產(chǎn)鎳生鐵的礦熱爐一回轉(zhuǎn)窯(RKEF)工藝的快速發(fā)展,我國不銹鋼原料逐漸轉(zhuǎn)變?yōu)橐糟t鎳生鐵、高碳鉻鐵為主,由于原料中含有較高的硅、磷、碳等元素,致使不銹鋼生產(chǎn)和使用受到制約。為此,太鋼根據(jù)市場原料變化,增加了中頻爐熔化設備,開發(fā)了多位一體不銹鋼生產(chǎn)工藝。
1主要設備狀況及生產(chǎn)能力
太鋼煉鋼二廠北區(qū)不銹鋼生產(chǎn)線于2006年底投產(chǎn),原設計產(chǎn)能為150萬t,經(jīng)過改造,增加了3臺50t中頻爐,1座180tAOD爐、1座180tVOD爐和1臺直弧型板坯連鑄機,2018年不銹鋼產(chǎn)量達320萬t,主要設備及工藝參數(shù)如表1.
2不銹鋼生產(chǎn)工藝流程
太鋼煉鋼二廠北區(qū)不銹鋼生產(chǎn)線原設計主要工藝流程為鐵水半熱裝工藝,如圖1所示。
2.1鉻系不銹鋼生產(chǎn)工藝流程
國內(nèi)越來越多的不銹鋼生產(chǎn)企業(yè)利用碳鋼系統(tǒng)的高爐供應部分鐵水給不銹鋼系統(tǒng),利用鐵水預處理脫磷冶煉不銹鋼,可提高鋼水質(zhì)量,有效降低成本。太鋼分別利用轉(zhuǎn)爐脫磷和鐵水三脫預處理脫磷裝置,結(jié)合中頻爐熔化高鉻,開發(fā)了以下三條鉻系不銹鋼生產(chǎn)工藝路線。具體如下:(1)180t轉(zhuǎn)爐鐵水脫磷→180tAOD冶煉180tLF/VOD→連鑄;(2)180t轉(zhuǎn)爐鐵水脫磷+50t中頻爐感應熔化高鉻→180tAOD冶煉→180tLF/VOD→連鑄(3)160t鐵水三脫預處理→180tAOD冶煉→180tLF/VOD→連鑄。
2.2鎳系不銹鋼生產(chǎn)工藝流程
2008年開始,我國逐步開發(fā)了以廉價的低鎳紅土鎳礦為原料的燒結(jié)一高爐工藝生產(chǎn)高磷鉻鎳生鐵和回轉(zhuǎn)窯一礦熱電爐(RKEF)工藝生產(chǎn)鉻鎳生鐵,降低了含鎳原料的價格。鉻鎳生鐵雖然價格低廉但存在雜質(zhì)元素(C、Si、P、S等)高的缺點.典型鉻鎳生鐵成分如表2。
為此,太鋼分析研究了鉻鎳生鐵原料特性,開發(fā)了電弧爐高效脫磷技術、AOD高效還原脫硫技術、電弧爐前期渣在線還原利用技術及AOD高效脫碳脫硅技術,形成了鎳系不銹鋼生產(chǎn)專有技術及多條不銹鋼生產(chǎn)工藝流程。主要工藝流程有:
(1)160t電弧爐熔化鉻鎳生鐵脫磷→160t電弧爐冶煉→180tAOD→180tLF/LTS→連鑄;
(2)50t中頻感應爐熔化高鉻+160t電弧爐熔化鎳生鐵→180tAOD→180tLF/LTS→連鑄;
(3)50t中頻感應爐熔化高鉻+50t中頻感應爐熔化鎳生鐵+160t電弧爐熔化鎳生鐵→180tAOD→180tLF→連鑄。
3多位一體不銹鋼高效冶煉工藝技術
3.1以鐵水為主原料的鉻系不銹鋼高效冶煉技術
3.1.1以轉(zhuǎn)爐脫磷鐵水為原料的鉻系不銹鋼生產(chǎn)技術
太鋼新不銹鋼工程投產(chǎn)初期,鉻系不銹鋼生產(chǎn)工藝路線為脫磷鐵水-電弧爐-AOD,工藝路線長,鉻收得率低,通過工藝優(yōu)化,開發(fā)了以轉(zhuǎn)爐脫磷鐵水為原料的新的AOD一步法鉻系不銹鋼生產(chǎn)工藝針對超低碳氮鐵素體不銹鋼的生產(chǎn),充分利用鐵水脫磷轉(zhuǎn)爐脫碳速度快的特點,提出了“脫碳任務再分配”的理念,即由“AOD+ⅤOD兩步法脫碳”演變?yōu)椤?/span>BOF+AOD+VOD三步法脫碳”,形成了新的超純鐵素體不銹鋼生產(chǎn)工藝,轉(zhuǎn)爐(BOF)完成鐵水預處理脫磷和AOD大部分脫碳任務,顯著改善了AOD的脫碳保鉻條件,提高了AOD生產(chǎn)效率。轉(zhuǎn)爐鐵水預處理時間比鐵水三脫預處理縮短了3035min,AOD精煉時間縮短了10-12min;中高鉻鐵素體不銹鋼的C+N總含量小于170×106.
3.1.2轉(zhuǎn)爐+中頻爐雙聯(lián)生產(chǎn)鉻系不銹鋼技術
煉鋼二廠北區(qū)鉻系不銹鋼生產(chǎn),采用轉(zhuǎn)爐脫磷鐵水,AOD冶煉過程中高碳鉻鐵全部在冶煉前期加入,高碳鉻鐵加入量大,吹氧脫碳過程鉻燒損嚴重,導致AOD還原硅鐵消耗偏高,鉻收得率偏低。為此,太鋼開發(fā)了轉(zhuǎn)爐+中頻爐雙聯(lián)不銹鋼母液生產(chǎn)鉻系不銹鋼工藝技術,利用中頻爐熔化高碳鉻鐵,熔化過程不會造成鉻元素損失,中頻爐熔化鉻鐵合金溶液兌入AOD冶煉,AOD人爐溫度提高,滿足吹氧脫碳保鉻溫度條件,可減少AOD吹煉元素燒損,提高鉻收得率2.47%,硅鐵消耗降低5.5kg/t,石灰消耗降低10kg/t;同時AOD每爐可加入10-15t鉻不銹鋼廢鋼,提高了AOD單爐產(chǎn)量,降低了噸鋼步驟費用,工藝優(yōu)化前后指標對比見表3.
3.2以鉻鎳生鐵為主原料的鎳系不銹鋼低成本冶煉技術
高磷鉻鎳生鐵具有較大的價格優(yōu)勢,在鎳系不銹鋼中大量使用可降低不銹鋼成本,但其中含有較高的PSi、S、C等殘余元素,含鉻鎳鐵水脫磷、高效脫硫、合理利用鎳生鐵中硅等成為不銹鋼冶煉的難題。針對存在的問題,分析了不銹鋼原料鉻鎳生鐵、高碳鉻鐵、鐵水等原料特性,研究了原料中Si、C元素優(yōu)化使用,利用中頻爐、電弧爐、AOD等工序進行多種組合,開發(fā)了鎳系不銹鋼低成本冶煉一系列相關技術,實現(xiàn)了低成本不銹鋼的生產(chǎn)。
3.2.1電弧爐含鉻鎳鐵水脫磷技術
由于不銹鋼生產(chǎn)流程中AOD及后續(xù)工序沒有脫磷能力,高磷鉻鎳生鐵的使用使得原料中磷含量大幅提高,為保證成品磷符合產(chǎn)品要求,必須在電弧爐或轉(zhuǎn)爐工序完成脫磷工作,而鋼水中鉻較磷易氧化,如何實現(xiàn)脫磷保鉻是一個冶煉難題。通過試驗摸索,采用CaO-CaF2-Cr03渣系脫磷,電弧爐脫磷渣系成分如表4.利用電弧爐脫磷動力學條件實現(xiàn)了電弧爐高磷鉻鎳鐵水脫磷,鉻收得率達到80%以上,脫磷率達到50%。圖2為308爐使用電弧爐含鉻鎳鐵水脫磷技術生產(chǎn)脫磷前后鉻和磷含量的對比情況。
開發(fā)了電弧爐熔化鉻鎳生鐵脫磷技術及電弧爐雙聯(lián)法冶煉不銹鋼預熔液生產(chǎn)鎳系不銹鋼工藝路線,脫磷電弧爐主要進行含鉻、鎳原料的熔化、脫硅、脫碳、脫磷,另一座電弧爐半熱裝脫磷鋼水進行不銹鋼母液的冶煉,然后再在AOD中進行精煉,冶煉過程中各工序鋼水成分如表5。
3.2.2中頻爐+電弧爐雙聯(lián)冶煉不銹鋼預熔液工藝
傳統(tǒng)鎳系不銹鋼采用電弧爐-AOD工藝路線,電弧爐中加入鉻鎳生鐵、高鉻、渣鋼等難熔固體原料,通電時間長,電極消耗高,鉻收得率低,電弧爐冶煉時間95min以上,電弧爐與AOD生產(chǎn)節(jié)奏不匹配。
太鋼開發(fā)了中頻爐+電弧爐雙聯(lián)熔化預溶液兌AOD冶煉不銹鋼工藝,電弧爐與中頻爐分別熔化不同種類爐料,中頻爐熔化高碳鉻鐵,鉻鐵沒有燒損,冶煉時間為70min,電弧爐主要熔化鉻鎳生鐵,電弧爐裝入量減少50t,電弧爐冶煉時間縮短為60min,電弧爐+中頻爐雙聯(lián)工藝技術的實施,實現(xiàn)了高碳鉻鐵與鉻鎳生鐵分工序熔化,縮短了電弧爐冶煉時間,實現(xiàn)了電弧爐與AOD節(jié)奏匹配。與原工藝相比,鉻回收率提高2.2%,電極消耗降低1.0kg/,大幅降低了不銹鋼冶煉成本。電弧爐雙聯(lián)工藝與常規(guī)工藝電弧爐人AOD成分及鉻收得率如表6。
3.2.3電弧爐前期渣在線還原利用技術
原工藝電弧爐原料主要為鉻鎳生鐵、高碳鉻鐵、廢不銹鋼等高鉻原料,電弧爐冶煉過程吹氧助熔,鉻元素燒損嚴重,電弧爐前期渣中Cr2O3含量較高(實測6%~10%)。一直以來,電弧爐冶煉不銹鋼都是將前期渣通過出渣門排人渣罐,在排渣過程中,不可避免在渣中會帶入一定量的鋼水,致使鉻收得率較低。
太鋼開發(fā)了電弧爐前期渣在線還原利用技術,電弧爐前期渣不再排入渣罐,而是排入中頻爐鉻鐵熔液的預熔包內(nèi),通過電弧爐出鋼時鋼流混沖攪拌,使高碳鉻鐵的硅與電弧爐前期渣中Cr2O3充分反應,還原渣中鉻,出鋼后利用鋼包大流量底吹氬氣進行強攪拌,實現(xiàn)鋼水中硅進一步與渣中Cr2O3反應,渣中C2O3含量由7.3%降低為2.5%,提高了鉻收得率,電弧爐前期渣與還原渣成分見表7。
3.24AOD高效還原技術
鉻鎳生鐵中硫含量較高,由于鉻鎳生鐵、不銹鋼渣鋼等原料使用量的不斷加大,使AOD入爐不銹鋼母液中硫含量不斷增加,達到0.06%以上,不銹鋼母液硫含量的升高給AOD脫硫帶來了困難,為此太鋼開發(fā)了AOD高效還原技術,通過選用合理的不銹鋼脫硫渣系,匹配還原渣堿度、還原時間以及還原期氬氣流量等參數(shù),開發(fā)AOD二次造渣脫硫工藝,實現(xiàn)了不銹鋼快速脫硫,AOD出鋼硫含量穩(wěn)定控制在0.005%以下,脫硫率達到95%以上。圖3為冶煉304不銹鋼2017年1~12月AOD鋼水人爐、出鋼硫含量及脫硫率。
3.2.5雙中頻爐+電弧爐三聯(lián)冶煉不銹鋼母液技術
近兩年來,電弧爐電極價格快速升高到15-19萬元/,電弧爐工序成本升高近一倍,降低電弧爐電極消耗可顯著降低生產(chǎn)成本。因此利用現(xiàn)有中頻爐設備,開發(fā)了雙中頻爐+電弧爐三聯(lián)法冶煉不銹鋼母液生產(chǎn)鎳不銹鋼工藝。采用一個中頫爐熔化高碳鉻鐵,另一個中頻爐熔化鉻鎳生鐵,兩個中頻爐熔化后的預熔液兌入電弧爐,電弧爐前期即可形成熔池,可提前吹氧脫硅,充分利用氧化放熱,降低電弧爐電耗及電極消耗,同時早期形成熔池,可減少電弧爐送電、吹氧過程對原料中鉻、鎳元素燒損。實際生產(chǎn)中,電弧爐熔化原料由120t減少為80t,鎳鋼電極消耗由2.28kg/t降低至1.52kg/t。
4結(jié)論
(1)太鋼充分利用現(xiàn)有裝備及廉價原料特性,開發(fā)了多位一體不銹鋼生產(chǎn)工藝,掌握鉻系不銹鋼、鎳系不銹鋼低成本生產(chǎn)關鍵技術,提高了產(chǎn)品競爭力。
(2)太鋼開發(fā)了廉價鉻鎳生鐵使用技術及工藝路線,實現(xiàn)了鉻鎳生鐵的大量使用,純鎳使用量大幅下降,鉻鎳收得率明顯提升,降成本效果顯著。
文章作者:不銹鋼管|304不銹鋼無縫管|316L不銹鋼厚壁管|不銹鋼小管|大口徑不銹鋼管|小口徑厚壁鋼管-浙江至德鋼業(yè)有限公司
文章地址:http://m.qbdsc.cc/Info/View.Asp?Id=1014
版權所有 © 轉(zhuǎn)載時必須以鏈接形式注明作者和原始出處
我們需要您的支持與分享
相關新聞
- 沒有資料